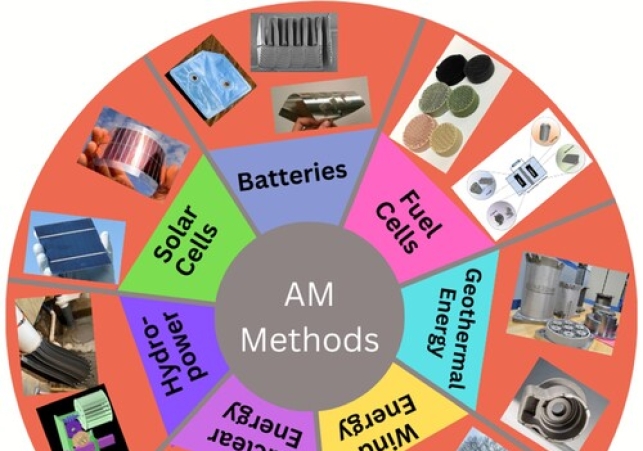
Additive manufacturing of selected ecofriendly energy devices
ABSTRACT
The burgeoning field of additive manufacturing (AM) applications has been extended to production of ecofriendly (green, clean, and renewable) energy generation and storage devices. Through a literature survey, the main energy generation and storage devices that produce little-to-no greenhouse gas emissions and their operational efficiency has been improved via AM manufacturing process were identified and discussed. The superiority of AM processes has led to the manufacturing of ecofriendly energy devices with geometrical precision and hierarchical porous interconnected structures that permit efficient diffusion of electrolytes and microbial population triggering ultrahigh rate operational performance which some have termed unprecedented. Despite the celebrated success demonstrated by the AM process, it is not in the mainstream of producing little-to-no emission energy devices due to the inherent limitations of the manufacturing process and the lack of industry-specific codes and standards to regulate AM-manufactured products. However, due to the automated nature of AM, it is expected that the current challenges inhibiting the adoption of AM into the main manufacturing stream will be addressed quickly by leveraging the synergy between artificial intelligence (AI) and AM for data collection and analysis.
1. Introduction
The agenda of reducing the global carbon footprint due to the over-dependence on fossil fuel to power the world economy has led to several proposals to move the entire global energy infrastructure to sustainable (ecofriendly) energy sources [Citation1]. These are a mix of energy-generating sources: Clean energy (clean air – little-to-no pollution), Green energy (no harm to the environment), and Renewable energy (sources that replenish naturally, such as the sun, wind, hydropower, and geothermal) that produce little-to-no greenhouse gas emissions during energy generation, storage, and operation [Citation2]. The attention of the research community and developmental agencies has been on all these energy generation sources and energy storage devices such as batteries that can store the energy generated from the various energy generation sources [Citation3]. Although there has been significant progress it also noted that the level of maturity and high production cost of these energy generation systems and storage devices may not permit them to replace fossil fuel energy systems completely in the short term [Citation4]. Thus, there is a need to accelerate their maturity and reduce their production cost using advanced technologies such as additive manufacturing which has the capacity to improve the operational efficiency of the various energy systems.
Additive manufacturing (AM) colloquially known as 3D printing has become an umbrella term denoting technologies that produce 3D structures with complex geometries layer-by-layer, and has already demonstrated its prowess as a renaissance of the manufacturing industry [Citation5]. The technology has demonstrated its agility by improving the efficiency and performance of most energy systems. A recent research breakthrough reveals that AM process was used to print solar cells that perform 20 times better as compared to conventional solar cells [Citation6]. The cells were 200 microns thin and estimated to cost 50% less than the current traditional manufactured solar cells. A collaboration at GE Renewable Energy led to 3D printing of tall wind turbines (200 m) to enable capturing of stronger winds that would translate into generating more renewable energy per turbine – thereby increasing the operational efficacy of the system [Citation7]. The AM process is used to produce intricate colling channel devices that weigh 50% less than conventional counterparts to increase the power density of energy-generating systems such as geothermal plants. The device demonstrates a higher operational efficiency and avoids flow restrictions due to AM capabilities to produce intricate features [Citation8]. The AM process has been used to produce batteries and fuel cells with interconnected circulatory networks of porous 3D structures of rigorous dimensional accuracy, permitting an efficient flow of communication between microbial population and electrolyte diffusion in cells – triggering unprecedented ultrahigh operational performance [Citation9, Citation10]. Based on such performance AM is touted to have the capacity to revolutionise the energy industry with unprecedented performance, which would be impossible using the conventional methods of manufacturing. An expert report also indicates that using AM to produce energy systems and devices could lead to more than 50% increase in the operational efficiency of most energy systems [Citation11]. The estimated contributions to energy savings demonstrated that AM process could revolutionise the energy industry by improving the operational efficacy of energy-generating systems, ensuring sustainable production, storage, and consumption. These unique features of AM have provoked consistent exponential growth in research outputs of using AM to produce ecofriendly energy generation and storage devices (Figure 1).
Figure 1. Number of publications in ScienceDirect of selected renewable/green/clean energy generation devices manufactured using AM methods (Data Source: Sciencedirect.com). (Note: Although different databased sources were accessed, only ScienceDirect data was used to plot Figure 1 indicating the growth of AM methods in the production of renewable energy generation devices).
Display full size
The concept of sustainable energy production and storage systems has made AM a preferred choice [Citation12], as the classical manufacturing methods are considered unsustainable in terms of carbon footprint, improving energy generation efficiency, improving energy storage capacity, wasting of materials, and complex supply chain management/costly transportation [Citation13]. The manuscript would focus on the contribution of AM in producing renewable energy systems and storage devices such as batteries which can store the energy generated and green energy devices such as fuel cells which are gaining dominance in replacing the use of fossil fuels in most internal combustion engines leading to the so-called ‘hydrogen economy’ [Citation1]. The capability of AM to generate clean energy in the nuclear industry would also be discussed. The ongoing intensive research in the nuclear industry is revealing that AM would possibly mitigate the long overdue debate regarding nuclear energy as clean energy as AM process is able to reprocess spent nuclear fuel – removing the actinides from spent nuclear fuel for reuse [Citation14, Citation15]. The current challenges, encouraging results, and the way forward using AM to produce these ecofriendly energy systems and devices that do not harm the environment would be discussed. The review would give insight into the pertinent future perspectives on how AM processes could contribute to the decarbonising of the environment via manufacturing of the energy generation and storage devices and expects to enlighten the research paradigm by giving a clear indication of the current stage of application of AM in producing energy generation and storage devices to assist in achieving the net-zero carbon emission agenda.
It is worth noting that the current review is focused on the role of AM in manufacturing ecofriendly energy-generating and storage devices and not on the detailed operational mechanism of the various AM processes. A detailed review of the various AM processes is well presented elsewhere [Citation16–18].
2. Am methods used for manufacturing energy devices
There are several energy generation, conversion, and storage methods; and AM processes have played a significant role in increasing the performance efficiency of various energy systems. As a result, there has been a consistent increase in the use of AM methods to produce energy generation and storage devices (Figure 1). There are many Clean energy (clean air), Green energy (no harm to the environment), and Renewable energy (sources that replenish naturally, such as the sun, wind, hydropower and geothermal) sources. Energy sources such as Biomass which lack consensus agreement as a renewable energy/clean/green source [Citation19, Citation20] are not considered. Only established renewable energy sources that showcase the undoubted potential of AM to boost the efficiency of energy generation systems and devices are considered (Figure 2). The focus of the current review is on established commercialised energy sources which are universally considered clean/green/renewable. Only established energy sources that showcase the undoubted potential of AM to boost the efficiency of energy generation and storage devices are considered (Figure 2).
Figure 2. Renewable/green/clean energy devices/components manufactured using AM methods.
Display full size
The committees on Additive manufacturing such as the American Society for Testing and Materials (ASTM) and International Organization for Standardisation (IOS) (ASTM/ISO 52900:2021) [Citation21] classified the AM technology into seven categories (powder bed fusion-PBF, vat photopolymerization – VP, directed energy deposition – DED, binder jetting – BJ, material extrusion – ME, material jetting – MJ, sheet lamination – SL). The AM systems have their unique capabilities and work with different printing mechanisms and materials to build a 3D structure.
Based on the data provided by Cherdo [Citation22] PBF machines are the most used currently in the AM manufacturing industry (Figure 3). This might be attributed to their unique capability to print virtually all AM material powder feedstocks into 3D structures with geometrical precision, better than other AM methods [Citation18]. DED machines are used mainly to repair/refurbishment components although they can also be used to print 3D structures. SL machines are used for joining dissimilar metals for a specific industrial application. BJ, ME, and MJ are commonly used to print non-metallic components such as polymers, ceramics, composites, etc. VP which comprised of AM systems such as Stereolithography, a digital light process that uses ultraviolet light to cure liquid polymers in a layer-wise fashion onto a part. The detailed operational mechanisms of the AM systems and their various feedstocks are thoroughly discussed elsewhere [Citation18]. Each of the AM technologies has machines registered under different trade names but uses the same or similar manufacturing principles (Figure 4). The uniqueness of the machine and the material feedstock they can produce enable them to print different components of renewable energy devices. They can work in a hybrid mode to print a renewable energy device monolithically [Citation23]. The AM machines have a wide range of applications (Figure 4) and can be used to print almost all the selected renewable/green/clean energy devices [Citation24].
Figure 3. The percentage use of AM machines to print metallic 3D structures (Data Source: Cherdo[Citation22]).
Display full size
Figure 4. Classification of AM technology based on material feedstocks, mechanism of printing, and manufacturing of energy generation and storage devices.
Display full size
As presented in Figure 5, batteries, solar cells, and fuel cells are the majority of energy-generation/storage devices produced by the AM methods, and PBF and VP are the most used to produce them. This might imply that there is a high market demand for these energy devices and the machines used to produce them. The perceived high demand for these devices could be due to their nature in terms of size and mobility. Batteries, solar cells, and fuel cells are mobile devices that can be easily transported from one place to another as compared to hydropower, wind, or geothermal energy plants, which are highly location-dependent and require governmental involvement to have practical investigations of such national/community-based facilities. As a result, the focus of academic researchers and industry practitioners shifted to investigating how to use the unique capabilities of AM process to enhance the energy-generating efficiency of batteries, solar panels, and fuel cells rather than capital-intensive stationary production renewable energy sources. Obviously, there are fewer hydropower, nuclear reactors or geothermal energy production centres compared to batteries, fuel cells or solar cells. Research on energy production machineries that are location dependent are normally conducted by large research institutes such as government-based research councils or via collaborations. Batteries, solar cells, or fuel cells research can be conducted by individual research clusters in most universities in a laboratory setting. As a result, there are many research outputs (Figure 1) on mobile energy generation devices. This intense research focus on mobile energy devices could also be triggered by incorporating miniature energy devices in watches, dresses, caps, coffee cups, etc. for intercommunication on the go – Internet of Things (IoT) [Citation25]. These might be the reasons why AM processes are heavily skewed towards manufacturing batteries, solar cells, and fuel cells compared to wind turbines, geothermal plants, nuclear plants, and hydropower components.
Figure 5. Application of AM for producing renewable/clean/green energy devices (Data Source: Sciencedirect.com). (Note: Although different databased sources were accessed, only ScienceDirect data was used to plot Figure 5, indicating the share of AM methods used in fabrication of the energy generation/storage devices).
Display full size
3. Applications of AM in ecofriendly energy generation and storage devices
3.1. The role of AM in batteries manufacturing
Most energy-generating devices could only generate energy while batteries have a dual capacity of generating energy and storing energy. Batteries are electrochemical devices that have the capacity to convert energy from a chemical state to electricity. Batteries are generally stacked of layers between the anode and cathode which makes AM process ideal for monolithically manufacturing a battery with unique properties and shapes that the conventional methods might not be able to produce [Citation17]. In the view of Sun et al. [Citation4], batteries are a fabrication of repeats layer stacking on each other – making AM the prime candidate for their fabrication. The versatility of AM permits the printing of customised thin batteries with improved operational efficiency (Table 1) that can be used in small devices such as backpacks, shoes, etc. Allowing objects that are used in everyday lives to communicate in Internet of Things (IoT) [Citation17] makes it suitable to contribute significantly to the fourth industrial revolution. Thus, the AM process has the capacity to print objects with embedded batteries [Citation5].
Table 1. Comparison of performance efficiency of AM batteries with conventionally (CV) manufactured batteries.
Maurel et al., [Citation31] demonstrated the possibility of using AM methods to print Lithium-ion batteries (LIB). Based on the structure of a battery: anode (current collector – copper, active material – binder, conducive agent, and solvent; separator/electrolyte; cathode (current collector – aluminium, active material – binder, conductive agent, and solvent) the printing feedstocks are normally transferred using an inkjet printhead, flexographic printing, screen printing, extrusion printing, stencil printing to print batteries layer-by-layer [Citation32, Citation33]. LiFePO4 (LFP) cathode was 3D printed by Liu et al. [Citation26] to be used in lithium-ion batteries. By adding 1,4 dioxane the LFP ink was frozen and solidified in the printing chamber to ensure mechanical integrity of the printed features and the shape of the cathode. The cathode was printed with optimised process parameters and allowed to dry to remove the solvent to obtain a highly porous architecture in the electrodes. The electrochemical performance of the 3D printed electrode was compared with a conventional manufactured electrode using roller coating. The results show that the porous architecture of the 3D-printed electrode greatly improved its performance. Electrochemical performance of 80 mAhg−1 was recorded for the 3D printed electrode and 61 mAhg−1 for the roller-coated sample [Citation26]. The authors conducted a similar investigation to produce three-dimensional unconventional electrodes with tailored geometries by varying the solid content, morphologies, and porosity and compared results with conventional roller-coating batteries [Citation28]. The results show that 3D samples with high solid content (≥0.467 g/mL) yielded a high electrochemical performance value of ∼82 mAh.g-1 while the roller-coated samples with low solid content (≤0.356 g/mL) yielded the highest electrochemical performance value of ∼60 mAh/g in its series. The comparison of various 3D-printed electrodes (Batteries) in Table 1 indicated that the AM process increases the operational efficiency of the batteries.
Using an extrusion-based AM process Li et al. [Citation27] 3D printed electrodes with a high aspect ratio to increase their mass loading in LiMn 2 O 4 battery and compared the results with conventional laminated batteries. The 3D printed batteries demonstrated high areal and specific capacity due to the novel interdigitated hybrid 3D structure. The 3D printed batteries demonstrated a high areal energy and power density for energy storage systems which could be used in the automotive industry and stationery energy devices. A performance capacity of 117 ± 6 mAhg−1 was recorded for the 3D printed samples compared to 110 ± 5 mAhg−1 for the laminated sample. Ao et al. [Citation29] developed a series of clog-free printable electrode inks for printing customised lithium-ion batteries (LIBs) and compared the capacity with conventional manufactured electrodes. The series of ink developed was used to produce Li4Ti5O12, LiNi0.815Co0.15Al0.035O2, and LiFePO4 electrodes via AM and roller coating. The electrochemical performance of the full cells assembled 3D printed batteries: Li4Ti5O12, LiNi0.815Co0.15Al0.035O2, and LiFePO4, were 158.3, 145.8, and 147.4 mAh g – 1 respectively compared to 152, 138.3, 140.8 mAh g – 1 for the conventional electrodes respectively. The AM process enables the printing of complex electrode structures demonstrating stable cycling stability and high-rate performance with low-cost printing strategy. Xu et al. [Citation10] 3D printed comb-like natural graphite electrodes with varying thickness and compared the performance to tape casted electrodes with the same varying thickness. The 3D-printed electrodes were tri-modally hierarchical porous structures with a porosity of 54.84%. At an optimal solid content of 50 wt% the electrode with 347.3 μm demonstrated the highest capacity of 451.1 mAh g – 1 at 0.1 C to 87 mAh g – 1 at 2.0 C compared to 339.4 mAh g – 1 at 0.1C to 24.1 mAh g – 1 at 2.0C for the tape casted electrodes. Based on LiMn0.21Fe0.79PO4 nanocrystal cathodes Hu et al. [Citation30] 3D printed a cathode with a coin cell to obtain an ultrahigh rate performance for the 3D printed cathodes and compared the results with traditional manufactured electrodes. The results reveal an impressive performance value of 150.21 mAh g−1 at 10 C for the 3D printed electrode against 103.38 mAh g−1 for the conventional sample and 140.67 mAh g−1 against 90.64 mAh g−1 at 20 C. Delannoy et al. [Citation34] went a step further to compare how ink-jet printing process affects the electrochemical performance of batteries with physical vapour deposition (PVD) method. A full Li-ion cell was 3D printed with LiFePO4 and Li 4 Ti 5O 12 porous composite electrodes and compared the performance with electrodes produced via PVD method. It is reported that the ink-jet printing electrodes demonstrated excellent electrochemical capacity of 145 mAh g−1 as compared to expensive PVD processes [Citation35]. Vernardou et al. [Citation36] also use fused deposition modelling to print graphene pyramids electrode for lithium battery with a commercially available PLA-based conductive graphene and compare the performance with flat printed graphene. A performance capacity of 265 mAh g−1 was recorded for 3D printed graphene pyramids electrode with retention of 93% after 1000 cycles. It was explained that the transfer of the Li+ across the graphene pyramids/electrolyte interface was easier as compared to the flat-printed graphene resulting in higher performance in the 3D-printed pyramids graphene electrode.
As presented above due to the fluidity of the feedstocks used in printing batteries with liquid or gel core, each layer must be dried before the process is repeated to print the batteries. Another major challenge of 3D printing batteries with solvent core is the temperature variation between materials such as ink for the anode and metal for the electrode. Intensive research is required to overcome the barrier of using ink feedstock and metallic feedstock in a monolithic manufacturing process. To increase the mechanical stability of a free-standing 3D printed battery, Kohlmeyer et al. [Citation37] increase the binder content in an active materials layer. The process led to brittle behaviour of the 3D printed batterie reducing the life span of the battery. It is also practically impossible to keep moisture in the atmosphere not to penetrate the battery during the printing process [Citation4]. For these reasons, conventional electrolyte solvents such as dimethyl carbonate, ethylene carbonate, ethyl-methyl carbonates, etc. are disadvantaged.
Solid electrolytes are normally used to print solid-state batteries (Solvent-free batteries) to improve conduction and reduce contact impedance [Citation38]. Phiri et al. [Citation39]. attempted to print free-standing electrodes for high-performing batteries. It was pointed out that the main disadvantage of the free-standing electrode is long-range lateral electron transport. Further research is required to produce metal-free standing batteries. However, with the emergence of hybrid manufacturing and multimaterial AM powder delivery systems, Sakuu Inc [Citation40, Citation41] a battery manufacturing company successfully demonstrate the superior manufacturing capability of AM process to produce ‘first-of-its-kind’ solid-state batteries in 2022. The solid-state batteries that were manufactured via binder jet printing and material jetting process demonstrated high energy density of 800–1000 Wh/L. The production of these next-generation SwiftPrint [Citation42] batteries has reached the milestone of mass production. This technological breakthrough has ushered in a new era in the history of energy generation, conversion, and storage. Thanks to the versatility of AM to print the lithium proprietary multi-material patterned battery with incorporated sensors, fixtures, and thermal transport pathways. The printing of solid-state customised Li-metal batteries at Sakuu Inc with high speed and low cost has transformed how batteries of the future will be fabricated via AM process (Figure 6). The AM approach led to a 44% reduction in factory footprint, lower capital expenditure by 23%, reduce operation process by 69%, and an overall reduction in manufacturing cost by 33% (Figure 6). The research and development units of Sakuu Inc [Citation40] have announced their vision of producing batteries with 200GWh energy output by 2030. The main advantages of solid-state batteries as opposed to batteries with gel core are that they have a longer service life span, shorter recharging time, greater energy density, freedom of design via AM methods – reduction in size and weight [Citation43]. The groundbreaking success of producing solid-state batteries [Citation40, Citation41] might eliminate the further research and development required to improve the efficiency of batteries such as lithium-ion batteries, zinc-ion batteries, lead – acid batteries that have a solvent core. Although these batteries have powered electric cars, phones, wearable electronics, cordless lives, etc. It could be predicted that research attention will shift entirely to improving the performance of solid-state batteries due to their obvious outstanding benefits.
Figure 6. Conventional battery manufacturing vs additive manufacturing of battery steps.
Display full size
Through an industrial collaboration, a lithium battery cathode and sodium-ion battery were developed using solvent-free LPBF processes. It is expected that the batteries would be used on electric buses to validate their efficiency in practice [Citation40]. The 3D printing of solvent-free batteries (Solid-state batteries) not only permits the customisation of the batteries but also enables the battery to form a structural component of the finished product [Citation42]. The use of the AM process ensures precise control over the amount of electrode and electrolyte materials, which enhances the energy and power densities of the batteries whiles enabling accurate design of the battery structure from the nanoscale to the macroscale [Citation44]. Zhang et al. [Citation45] focus on understanding the impact of the various 3D-printed electrode/electrolyte structures on the performance of solvent-free batteries. Their report reveals that the optimisation approach of AM process enhanced the utilisation of internal space, electrode surface area and improved the electrochemical performance of 3D-printed batteries. The development of solid-state batteries or green batteries required the development of new materials. Recently, a group of researchers has been tasked to print batteries using lunar and martian regolith materials that are only available on the moon. This is an initial experiment on the possibility of printing green batteries on the moon [Citation46]. 3D printed batteries generally use about 40% less material, charge in minutes, and are easily recyclable, which supports the idea of green manufacturing of batteries [Citation17]. The 3D printing of solid-state batteries would trigger a quantum leap in the energy density of batteries and drastically reduce the cost of battery fabrication.
3.2. The role of AM in fuel cells manufacturing
A fuel cell (FC) uses electrochemical reactions to transform the chemical energy in a fuel and oxidant into electricity without the need for intermediate thermal or mechanical processes [Citation1]. AM processes have been used to produce various components of fuel cells with large reaction areas and intricate membrane geometry of high conductivity and performance (Tabel 2). Multiscale porous structures were produced for use in various types of fuel cells including polymer electrolyte membrane (PEM) fuel cells, biological fuel cells (BFC), reversible fuel cells, Microbial fuel cells (MFC), etc. [Citation1]. The AM components enhance the efficiency and amount of electrical energy generated by the fuel cells [Citation47]. Using the advantage offered by AM a Calignano et al. [Citation48] printed a fuel cell with coral skeletal structure geometry network woven channels circulatory system that allows communication between the microbial populations (electrode bioconsortia) – enhancing the transfer of electrons abetween the biofilm and the electrode network. The well interconnective in the cell (Figure 7(a)) due to its intricate nature led to the generation of a power density of 2500 mW m−2 compared to 816 mW m−2 produced by conventional manufactured fuel cells [Citation49]. Due to the unique geometrical configuration of the cell, it was able to produce optimal energy recovery of about 3 kWh m−3 per day. The authors concluded that the fuel cells can be used to power sensors and low-power appliances and can be used in in harsh environments.
Figure 7. (a) Lattice structure with a node [Citation50]; (b) MFC 3D printed anode and inner cathode [Citation51]; (c) Schematic representation of the internal structure and 3D printed bipolar plate [Citation52]; (d) Topology optimisation additive manufactured fuel cell end plate [Citation53].
Display full size
Titanium liquid/gas diffusion media was also produced via EBM by Mo et al. [Citation54] to demonstrate the capability of AM to produce proton exchange membrane electrolyser cells (PEMECs) with well-controlled multifunctional parameters. Compared to the classical woven liquid/gas diffusion layers, the AM fabricated liquid/gas diffusion layers demonstrated higher performance due to a large reduction of ohmic losses. The EBM fuel cell demonstrated high corrosion resistance, well-tunable multifunctional parameters, fast manufacturing, controllable pore morphology and structure, and economic as compared to the convention fuel cell with an 8% increase in performance efficiency. The high-performing capability of the microbial fuel cells is due to the AM process to produce a network of channels very similar to circulatory systems in the 3D metal anodic structure [Citation55]. The corrosion resistance is due to the inherent passivation or re-passivation process nature of titanium and its alloys to form extremely thin, stable, and adherent protective titanium oxide film in an oxidation medium [Citation56]. This passivation or re-passivation process makes titanium and its alloys favourable to produce liquid/gas diffusion media since they would perform excellently in such a harsh environment.
The literature demonstrated that AM processes could be used to produce cellular/lattice structures with pore sizes in ranges of 100 μm, porosity (>0.9) with good permeability for sufficient thermal/electric conductivity [Citation57], indicating that the AM process has attained maturity for manufacturing intricate structures for FCs [Citation58]. It is reported that biological FC has demonstrated great competitiveness in the energy sector probably due to the capability of AM process to produce intricate structures for hosting microbes that could produce enzymes for energy conversion through biological metabolisms. Bian et al. [Citation59] use the AM process to produce MFC of 3D architecture with controllable pore sizes using a UV-curable resin and reported a 10-fold higher power density and 3-fold larger maximum voltage as compared to similar MFC of copper mesh electrodes. The maximum voltage of the 3D-printed interconnected cell was 224.5 ± 32.4 mV while that of the mesh fuel cell was 179.1 ± 22.8 mV. In a similar study, Bian et al. [Citation60] used the AM process to print a porous carbon anode to enhance power generation in MFC. Comparing the results obtained from the 3D printed cells to carbon cloth anode and carbon fibre brush anode under the same condition. It was indicated that the operational efficiency of the 3D cells increases due to a larger surface area that improved the bacterial adhesion, excellent biocompatibility, and better mass transfer leading to the highest maximum output voltage of 453.4 ± 6.5 mV and power density of 233.5 ± 11.6 mW m−2. He et al. [Citation61], 3D printed a hierarchical pores MFC with functionalised modular electrode materials to demonstrate high-performance bioanodes in bioelectrochemical systems. An unprecedented high volumetric current density of 10,608 ± 1,036 A/m 3 was recorded. The high performance was attributed to the high specific surface area that enhances bacteria attachment and inter-facial electron transfer. The result was 7.9-fold higher than the control carbon-felt bioanode (10.8 ± 2.2 A/m 2) of the same thickness. Freyman et al. [Citation62] went a step further to demonstrate the possibility of printing living and functional 3D bacterial structures as a living electrode for a FC. The preliminary investigation has opened an array of research to understand the interactions among bacteria strains, electrode materials, and surrounding environments in a FC. Theodosiou et al. [Citation63] used AM to speed up the process of manufacturing a fuel cell and reported a maximum power output of 286 μW, for the 3D printed cell compared to a conventional fuel cell of 85 μW power output.
You et al. [Citation51] focus on improving the performance efficiency of microbial fuel cells (MFC) and lowering the cost of production by 3D printing the anode, cathode, and chassis with low-cost, biodegradable polylactic acid (PLA) material (Figure 7(b)). The monolithic manufacturing of the MFC eliminates complex assembling process, avoiding of human error that would ensure consistent performance (repeatability and reliability) introducing cost effectiveness which would drive commercialisation of MFC technology. The 3D printed cell demonstrated higher power output levels (520−570 μW, 7.4−8.1 W m−3) compared to the control-modified carbon veil classical manufactured cell (376.7 μW, 7.5 W m−3). The 3D printed cell with improved operational efficiency was used to power digital weather station successfully. The same authors use the high degree freedom of AM to produce the membrane and anode of MFC with commercially available printable polymer (Gel-Lay) and recorded a maxim power output of 240 ± 11 μW which is 1.4 times higher than the control 177 ± 29 μW commercially available cation exchange membrane (CEM) produce with the conventional method [Citation64].
Microfuel cells with an active area of less than 1 cm2 were produced by Scotti et al. [Citation65] with stainless steel using the versatility of LPBF process. The authors noted the possibility of monolithically manufacturing the micro-FC in one manufacturing cycle. The micro-FC generates a high-power density of 238 mW cm−2 and a current of 1.2 Acm– 2. It is reported that the fuel cells demonstrated 65% practical efficiency as compared to other FCs of similar series [Citation66]. Agudelo et al. [Citation9] replaced a carbon-based gas diffusion layer in Tubular High Temperature Proton Exchange Membrane Fuel Cells with porous thin-walled 316L stainless steel manufactured via LPBF process. Using hydrogen as the fuel and air as the oxidant the operational efficiency of the 3D-printed cell was tested through electrochemical characterisation. The results reveal that the metal substrate FC with 16% porosity demonstrates a higher performance peak power density of 329.25 W/m2 at 125.52 A/m2.
AM processes could be used to produce a bipolar plate (Figure 7(c)), which is the backbone of FCs. The bipolar plate of a fuel cell ensures uniform distribution of gas and removal of water through the gas flow channels, separates the individual cells, conducts current between the individual cells, and provides a supporting mechanism for the FCs [Citation67]. Jin et al. [Citation68] produced a bipolar plate with stainless steel via LPBF process to increase the fuel cell performance. The bipolar plate was manufactured with an innovative flow field design termed triple serpentine flow field. The serpentine flow field demonstrates a current density value is 1.2052 A/cm2 at 0.6 V, which is 52.8% (0.7888 A/cm2) higher than bipolar plates with rectangular channels and 24.9% (0.9652 A/cm2) higher than graphite bipolar plates produced with the classical method. Wang et al. [Citation47] investigated the strength and electrical conductivity of bipolar plate of fuel cells produce via laser sintering by introducing 26 volume percent chopped carbon fibre. The authors reported that the flexural strength of the cells improved by 40%. To increase the production rate of bipolar plates’ use in creating the stacks in FCs, new scanning strategies are being developed to speed up the printing process of bipolar plates for hydrogen fuel cells by incorporating tailored beam shapers. The new scan arrangement has the potential for efficient mass production of bipolar plates according to the requirements of the US Department of Energy (DOE). Gould et al. [Citation69], used the laser powder bed fusion process to produce fuel cell bipolar plates and indicated that further research is required to reduce the size, weight and increase the flatness of bipolar plates for large FC stacks, despite the advantage offered by the AM process to speed up the development process and reducing the cost by eliminating tooling and welding process. Herzog et al. [Citation53], produced an end plate for a fuel cell with AlSi10Mg and Ti-6Al-4V powders via LPBF process (Figure 7(d)). Using a topology optimisation approach the AM end plates resulted in a 48% weight reduction with improved performance in electric stack power due to the uniform distribution of the contact pressure ensuring optimum electric conductivity over the series connection of cells. The maximum electric stack power obtained from the topology-optimised end-plate was 107.8 W at 45 A (Table 2).
Table 2. Comparison of performance efficiency of AM fuel cell with conventionally (CV) manufactured fuel cell.
The anode off gas recycle blower that supports the fuel stack of solid-oxide fuel cells was 3D printed [Citation71]. Using AM to print the anode off gas recycle blower of the cell has increased the aerodynamic efficiency of the components achieving higher-performance rotating turbomachinery designs at a lower cost [Citation72]. The AM process drives the cost of the device from $15,000 to $500 [Citation73]. Despite the cost-saving advantages offered by AM process, it was reported that the surface roughness of the AM samples was a major drawback although the product is currently commercialised and is being used by many corporations. The one-cycle step manufacturing capability of AM processes eliminates the assembling process and completely removes clamps, gaskets, screws, clips, sealants, etc. [Citation74], which simplifies the manufacturing process and the lead time to market for fuel cells [Citation75]. One of the main reasons for the intensive ongoing research to improve the performance of FC while reducing its manufacturing cost via advanced technologies such as AM is that the only by-products from the fuel cell reaction process are water and heat [Citation1]. The high demand for FC, especially FC that operate at relatively low temperatures (70 to 90°C) and pressure (1–2 bars) [Citation1] is their capability to power the manufacturing and automobile industries with reliability and durability without carbonising the environment [Citation76]. The strict regulations forcing the automobile industry towards a complete ban on internal combustion engines using fossil fuels by 2050 in most developed countries, is also contributing to the rapid growth in research and development of renewable/green energy devices. Passenger modes of transportation account for more than 50% of the global energy demand by the transport sector while it is estimated that the number of passenger vehicles worldwide would increase from 1 billion to 2.5 billion by 2050 [Citation77]. This will cause an increase in greenhouse gas emissions if an alternative approach is not found to propel these energy-hungry machinery that transport passengers. The adoption of green/renewable energy devices to replace the current powering systems in the automotive industry depends on several factors as indicated in Table 3. Further research is required to reduce the operational cost of these eco-friendly energy devices, increasing the charging rate of batteries, and the efficiency of fuel cells among others, which AM is contending to achieve.
Table 3. Comparing fossil fuel energy to alternative clean/renewable energy.
3.3. The role of AM in solar cells manufacturing
Solar cells are electronic devices that generate electricity by converting solar energy from photovoltaic (PV) effects in the presence of sunlight [Citation79]. The energy is generated by absorbing quantised energy (photons) to produce charge carriers, which are collected at their respective contacts. Solar technology will aid ecological sustainability and the creation of a carbon-free world [Citation1]. However, due to the initial high cost of investing in solar energy generation, the records reveal that solar energy usage contributes to only about 2% of the world's energy usage. It is only in a few advanced countries that 7% of the energy source is attributed to solar energy. For the adoption of solar energy to be competitive with the conventional electricity source the price per kWh of solar energy needs to be reduced. This could only be achieved through less expensive manufacturing routes and the use of cheaper non-toxic materials compared to the current silicon wafer technology [Citation80]. The current silicon solar panels need to be replaced despite purported energy freedom and money-saving theories. Apart from its initial high upfront costs and large space requirements – its environmental impact is another major concern. The current reports reveal that it takes about 130 litres of oil to produce a single silicon solar panel and it is estimated that by 2050 about 78 million metric tons of solar panel waste will find their way to various landfills around the globe [Citation81]. This alarming concern could be eased by using recyclable materials via 3D printing to produce novel solar cells with geometrical configurations that could improve the harnessing of solar energy at a lower cost [Citation82]. Firtina [Citation83] reported that polyethylene terephthalate (PET) is used to print solar cells on a plastic film of less than 0.1 mm as compared to conventional solar panels that are ten millimetres thick. The 3D-printed solar cells are ultra-flexible, lightweight, recyclable, and less expensive as compared to conventional solar panels.
Researchers at MIT [Citation84] reported that using AM technology, they were able to design solar cells (Figure 8(a)) that demonstrated efficiency in power generation by a factor of 20 compared to the conventional flat-laying PV panels on a roof and environmentally friendly material (PET) was used to print the solar panels [Citation85].
Figure 8. (a) A thin paper-like solar cell [Citation86]; (b) A 3D-model of a light trap with a concentrator at the top of the cage and solar cell at the bottom (cell area shown in red). The reflected light from the solar cell is recycled within the cage [Citation87].
Display full size
The AM process was used to print semiconducting ink on a thin layer of 200 microns to replace the old fashion toxic PVs. The thinness of the AM solar cells implies less material usage, and less emissions reducing the carbon footprint. The current techno-economic analysis reveals that AM process can reduce the price of solar cells by 50% [Citation43] just as indicated in the groundbreaking research report of MIT [Citation88]. Bernardi et al. [Citation89] also mounted Si solar cells on AM-fabricated frames with optimised geometries. Their investigations reveal that the AM module demonstrates higher densities per projected area (kWh m−2) by a factor of 2–20 than stationary flat PV panels and an increase in energy density by a factor of 1.5–4. These studies prove that AM solar cell modules could mitigate the seasonal, latitude, and weather variations which are inherent variability in conventional solar PV cells. The AM approach demonstrates an even generation of solar energy at all latitudes, doubling the peak power generation hours as compared to flat panel design. Using AM processes in harnessing solar energy could usher in Terawatt-scale generation of solar energy, which could be used for domestic and industrial applications without carbonisation of the environment [Citation90]. It is also reported that using biomimetic inspirations to print honeycomb structures to produce micro-solar cells using carbon-neutral materials recovered from discarded solar panels generated energy power density three times higher compared to conventional silicon-based solar cells [Citation85]
AM has a great role to play in the quest to migrate from fossil fuel to green energy generation. AM could also assist in rapid manufacturing. Conventionally solar cells are experimented on by analysing the solo cells embedded in the panel. AM could be used to produce the module and the solar cells in one manufacturing cycle for analysis, which will speed up the experimental process. The success of AM is that it can drastically increase surface area without increasing footprint. AM probably offers a facile route for improving the conversion efficiency of photovoltaic and photo-thermal modules. Huang et al. [Citation91] use AM to print dye-sensitized solar cell modules designed with intricate features. The photovoltaic efficiency of the module improved from 5.48% to 7.03%. Van Dijk et al. [Citation87] also printed hexagonal and circular parabolic concentrators with a light cage to demonstrate external light trapping and reported an effective path length enhancement factor larger than 2 with a 69% improvement in the external quantum efficiency and a 15% enhancement of the energy conversion efficiency (Figure 8(b)). The customisation of light-trapping metamaterials and the development of designed surfaces in order of 200 nm using AM processes, demonstrated recently by Knott et al. [Citation92] for light management in solar cells paved the way for increasing energy generation. It is also pointed out that the inability of AM to fabricate the light-trapping parts with a high-aspect-ratio necessitates further research attention to bring the technology to the commercialisation stage [Citation80]. It is expected that the automated nature of AM, which permits the use of artificial intelligence tools in the design process will assist in optimising light trapping and light concentration structures that will speed up the commercialisation readiness of the technology. The capability of AM to print high-throughput large-scale roll-to-roll photo voltaic (PV) thin-film solar cells on flexible substrates [Citation93] gives the indications that AM could be used to print the next-generation lightweight solar cells nano-, micro-, and macro-structures. Tarancón et al. [Citation80] noted that all solar cells could be printed monolithically in one manufacturing cycle via the AM process what is required is the optimisation of the current manufacturing process to provide commercial feasibility which could enable the printing of mobile solar cells, disposable solar cells, solar cells printed on textiles, solar cells for use in sensors, actuators (IoT). As a proof of concept, Mathies et al. [Citation94] use noncontact inkjet printing to print a high-efficiency perovskite solar cell. The perovskite solar cell demonstrated a constant stable power conversion efficiency of 12.9% compared to conventional solar panels. The rapid digital deposition methods used permit excellent control over the layering structure leading to good connectivity between the light-absorbing layers.
3.4. The role of AM in hydropower generation
Hydropower-generating plant converts the kinetic energy from running water into electricity [Citation95]. The water level and the flowrate determine the amount of electrical power generated by the plant. Records reveal that currently hydropower accounts for approximately 47% of the renewable energy source in the world, which is the largest contributor to renewable energy sources [Citation96]. However, it is also stated that since hydropower is one of the oldest renewable energy technologies most of the components are no longer in stock since the manufacturers are no longer in business or have diverted to other latest technologies. As a result, replacing damaged components of hydro dams is becoming difficult. Such scarce spare parts are normally candidates for AM. A corroded log-boom anchor for the Nimbus Dam near Folsom in the United State California was redesigned using topology optimisation techniques and 3D printed, employing a Concept Laser machine, since it became almost impossible to find spare parts to repair the old-age dam. The components of the log-boom anchor were reduced from three to one and the total mass of the structure was reduced by 50% with about 150% cost reduction. A collaboration between Oak Ridge National Laboratory (ORNL), and AMJET Turbine Systems led to the manufacturing of Axial Flow Hydropower Turbine Housing, Runner, and Draft Tube using different AM processes for ATS-8 turbine to be installed on Keokuk Dam [Citation97]. The components of most old dams around the globe are currently replaced by 3D-printed parts using the like-for-like printing replacement strategy. Takagi et al. [Citation98] used AM to print spare parts to improve the Japanese hydropower-generating technology, which was commercialised in the 1920s. AM was used to improve the functionality of a waterwheel of a plant. It is also demonstrated that the turbine runners (Figure 9(a)) of dams can be printed using AM technology [Citation99]. Andres et al. [Citation95] developed a 3D-printed Pelton Turbine for a Pico-Hydro electric generator (Figure 9(b)). The device could generate 350 W to 400 W output power. Pico hydro generators are 3D printed from sustainable materials based on recyclable plastics that generate electricity for domestic and industrial consumption. Lee et al. [Citation100] use AM processes to print a controllable-pitch Archimedean screw for pico-hydropower generation. The performance evaluation indicated power generation of 123 W and 71% in 0.04 m3/s efficiency. The versatility of AM was used to print bladeless portable lightweight hydraulic turbines [Citation101]. The ongoing 5 billion kWh of Yangku Hydropower Plant in China, which is being constructed via AM process using an automated robotic system (AI) demonstrated the maturity of using AM to construct the next generation hydropower plant [Citation102].
Figure 9. (a) 3D – CAD outline of turbine [Citation99]; (b) 3D printed turbines [Citation95]; c) Packer systems [Citation103].
Display full size
3.5. The role of AM in geothermal energy generation
The main advantage of using AM to produce geothermal energy machinery is that AM could be used to produce specialised drilling tools required for accessing geothermal wells at a lower cost with higher efficiency [Citation104]. The specialised drilling tools that can operate in harsh subsurface environments are produced in small quantities due to the niche nature of the geothermal sector at a very high cost using the classical methods of manufacturing [Citation105]. Since the customised drilling tools for harsh geothermal environments are made in low volume, they are prime candidates for AM. Manufacturing downhole tools like long bars or tubes using conventional methods required special holding setups to avoid warping and vibration for complex and fragile components with small diameters and long lengths. Some setups are destroyed during the machining process and need to be reconstructed making manufacturing of geothermal tools very costly, time-consuming, and complicated process via the conventional methods [Citation105]. AM processes could be used to produce customised drilling devices at a lower cost. It is estimated that geothermal energy has the capacity to offset the overdependence on fossil fuels with its associated challenges. However, overcoming the first hurdle of producing specialised machinery that can operate safely and efficiently beneath the earth under harsh environmental conditions and extracting energy from geothermal wells is the main challenge [Citation106]. The ability of each tool to withstand extreme temperatures, high pressures, corrosive substances, and drilling through nearly indestructible rocks to tap the energy beneath the earth's surface required the selection of the right material and the manufacturing route [Citation103].
Due to the low-volume nature of geothermal tools production, it often leverages the oil and gas industry's supply chain to reduce production and inventory costs [Citation104]. This approach can cause unnecessary operational delays when specialised tools are required for special purposes in the geothermal fields. To overcome such constraints, Downhole Emerging Technologies [Citation105] used the superior manufacturing ability of AM to print a packer system in Inconel 718, 316L, and 17-4 stainless steels that can deform, precisely and rapidly, creating a seal in the mine shaft at extreme temperatures within the well (Figure 9(c)). There are embed sensing devices in the packer system which could only be achieved via using AM processes to ensures less force is required to compress, stretch, unset or retract but getting a higher output as compared to the previous conventional manufactured packer system [Citation107]. The inventors noted that the novel packer system is just not a hollow ring, but with very complex internal embed features which is impossible to achieve using the classical approach to obtain such structures to access the geothermal well. It is purported that with the invention of the current metal packer system that is intended to replace the previous rubber and plastics packers system which has limited capability to withstand the harsh environment, it would be possible to unlock significant geothermal energy to contribute to the decarbonisation of the environment [Citation105, Citation108].
Recently in Italy, a geothermal well machinery (impeller) that was supposed to end up in a landfill because the components could not be fixed with conventional forging techniques, was repaired via AM process. Repairing the impeller via AM, an essential component of the centrifugal compressor, saves about €70,000 per annum [Citation104]. It is indicated that although wind, hydropower, and solar power are also renewable energy sources they are position-dependent and have demonstrated more unreliability due to the intermittent nature of wind and solar [Citation109]. Geothermal energy sources could be considered to be stable with high thermal efficiency since they are not affected by climatic fluctuations making them reliable renewable energy sources that should be considered for the future [Citation108]. The is a need to critically identify the role AM can play in increasing the efficiency of geothermal energy because geothermal energy is conceived as undeletable on a human time scale [Citation110]. The report of Kumar et al. [Citation110] shows that the availability factor of geothermal energy is 2.4 times higher than biomass, 2.2 higher than wind energy, and 1.3 times higher than solar energy, indicating its reliability which is not affected by fluctuating climatic conditions.
In the view of Price et al. [Citation111] although geothermal machinery for reservoir characterisation, construction, and operations are classified as technology-intensive – the tools for geothermal energy exploration are similar to those used in oil and gas exploration. Because of the similarity between the machineries used in the two fields; downhole tools and drilling equipment tools used in the oil and gas industry could be adapted for the harsh geothermal environments. The low-volume production of specialised sophisticated tools for geothermal energy exploration is often cost-prohibitive, which could be resolved via AM processes. The niche nature of geothermal exploration makes the research on manufacturing geothermal machinery still at the nascent stages. The prototype nature of AM could be used to speed up the research and industrialisation of next-generation geothermal wall tools.
It is also mentioned that AM could play a great role in improving the efficiency of the supply chain in the geothermal plants by providing the possibility of manufacturing spare parts onsite facilities since most plants are in remote locations from parts manufacturing centres. A huge inventory is normally kept onsite to mitigate equipment downtime in order to ensure quick repairs during a machinery breakdown [Citation112]. Keeping a large inventory is a complex supply chain process, the potential of AM to produce parts on-demand can eliminate the herculean tasks of managing a complex supply chain through a decentralisation process since broken parts can be quickly improvised onsite which provides significant benefits on cost-saving. It is pointed out that AM process might have disruptive effects on the supply chain rather than production cost or part performance [Citation112, Citation113]. This statement was made in lieu of the increasingly isolated nature of plants. Due to the rapid advancement in technology components become absolute or changes in standards make it difficult to obtain spare parts for breakdown machines in remote areas. AM process could be used to provide a like-for-like replacement cutting out the complex shipment/transportation process which would translate into a reduction in greenhouse gases to achieve the much-desired carbon-free world [Citation112]. There is intense ongoing research on embedding sensors into geothermal machinery to monitor the structural health of the wells as well as functional systems like energy harvesting devices, circuits, and piezoelectric actuators to access relevant information for decision-making [Citation109]. Although these imaginative technologies are attracting a significant volume of research and good early days results; there are major technological and regulatory hurdles to overcome before releasing their commercial and economic gain.
3.6. The role of AM in wind energy generation
According to the Global Wind Energy Council [Citation114], there is exponential growth in the demand for wind energy generation. However, there is a need for the development of new materials and manufacturing approaches that would reduce the cost of the technology to ensure the industry grows continuously and the demand continues to increase [Citation114]. Besides hydropower energy sources (47%), wind (25%), and solar (23%) are the largest sources of renewable energy used in the world [Citation115]. Globally, the proportion of wind and solar energy has increased considerably by about three-fold from 2010 to 2018 [Citation114]. The International Energy Agency reports reveal a 2.4% increase in global energy demand; and wind, wave, and tidal renewable energy sources have a crucial role to play in mitigating the greenhouse gas effect. This is evident in the 14% increase in wind-based energy generation globally [Citation116].
Different industry and academic collaborations are ongoing to improve turbine blades and moulds for wind, wave, and tidal energy generation using AM. AM processes are used to print concrete-based anchors and turbine substructures. AM systems are specifically designed to print large full-sized moulds for turbine blades using a cheaper biopolymer (Figure 10(a)). GE has used AM to print turbine towers and lighter turbine blades for energy generation [Citation117] The heights of the turbines are normally limited to about 100 metres due to the difficulty of transporting a pre-built column by road. With AM it would be possible to build turbines to a height of about 200 metres (Figure 10(b)). A higher altitude for a turbine implies higher performance. For instance, for wind turbines – wind speed tends to pick up at higher altitudes. GE reported that AM could be used to increase the competitiveness of both onshore and offshore wind energy generation by reducing costs and eliminating complex supply chain management [Citation118]. AM-printed turbine blade tips from thermoplastic composites have proven to be lighter than their conventionally manufactured counterparts. Their lightweight nature enables the use of larger rotors on turbines that have improved the performance efficiency of the turbines. The lightness of the turbines increases the longevity of the turbines by reducing strain on the entire structure.
Figure 10. (a) 3D printing of large wind blade moulds [Citation119]; (b) 3D printed tall turbine towers [Citation7]; (c) 3D printed rotor blade [Citation120]; d) 3D printed turbine blades [Citation121].
Display full size
A collaboration between Renishaw and Nova Scotia Community College (NSCC) in Canada led to the manufacturing of PowerCone retrofit that co-rotates with the turbine’s rotor and curved propellors via AM with an 80% reduction in cost of manufacturing [Citation122]. Rouway et al. [Citation123] used AM to produce tidal and wind turbines with thermoplastic polymers that were reinforced with carbon and glass fillers. The thermomechanical analysis demonstrates low mechanical deflection and warpage, indicating an excellent opportunity of using AM to produce turbine blades. Murdy et al. [Citation124] 3D printed composite tidal turbine blade in which the composite mould forms part of the final load-bearing structure. The capability of AM to produce blades with single-piece construction and embedded root fasteners is an avenue to explore for the next generation of turbine blades. To minimise the effect of excessive noise and vibration, a turbine rotor blade and a skew was introduced at different angles. The rotor was 3D printed and the results reveal that a highly skewed rotor had significantly lower drag and torque fluctuations. It was concluded that the 0-degree skewed rotors are more hydrodynamically efficient as compared to the 90-degree skewed rotors. A software coding – ROTORYSICS reveals that cavitation rarely affects turbine rotors while for hydrokinetic turbines installed on dams in rivers and waterfalls, cavitation normally affects their performance and life span [Citation120]. Finnegan et al. [Citation125] proved that using AM to produce wind turbine blades with fast change in geometry over a short length could enable the blades to operate efficiently for more than 20 years (Figure 10(c)). The AM-built blades demonstrate a high capability of withstanding high mechanical loadings, both static and fatigue which would reduce maintenance costs and allow the generation of uninterrupted energy.
AM permits the optimisation of the blade parts configured according to a particular area's wind and grid resources. Oak Ridge National Laboratory [Citation126] is experimenting on 3D printing of permanent magnets on wind turbine generators. The aerodynamic requirements of turbine blades require a complex geometrical design (Figure 10(d)) which makes AM a prime candidate for producing turbine blades for the wind, tidal, and wave energy generation systems [Citation127]. Large turbines are difficult to manufacture due to their unique requirements [Citation128], thanks to the capability of AM to print large moulds (Figure 10(b)) for the turbine blades, used in wind energy and tidal energy industry. The AM process reduces the cost and time-to-market of manufacturing the moulds. To eliminate greenhouse emissions and reduce the cost of manufacturing turbine blades researchers are experimenting with using a biopolymer derived from wood to print turbine blades rather than the conventional carbon-fibre-reinforced ABS material. Eco-friendly turbine blades have been 3D printed with recyclability material after their service life [Citation129]. AM is also used to perform repairs and maintenance of turbine blades.
3.7. The role of AM in nuclear energy generation
The main desire for the use of AM processes in the nuclear industry is the capability of AM technology to produce 3D structures with multimaterial properties (Figure 11(a)). The technology has the capacity to strategically deposit different materials discreetly in a 3D structure according to the intended applications pricelessly at specific locations [Citation5]. The compositional gradient of materials makes the AM ideal for nuclear plants since there are distinct variations in radiation doses, pressures, and temperatures that require different material properties in the same nuclear plant unit [Citation4]. Using the multimaterial manufacturing process to produce nuclear plants will permit variations of material properties/gradients at an arbitrary interior point within the nuclear plants in a monolithic manufacturing cycle.
Figure 11. (a) 3D printing of multi-materials [Citation130]; (b) 3D printing of nuclear thermal propulsion chamber [Citation131]; (c) 3D printed GRCop-84 combustion chamber [Citation131]; (d) Mass-optimised AlSi10Mg cryogenic propellant injector [Citation131]; (e) 3D printed thruster [Citation131]; (f) 3D printed integrated heat exchanger [Citation131].
Display full size
The approach of using AM to manufacture nuclear plant components for energy generation would bring the advantages of narrow fusion zones with minimised heat-affected zones as compared to conventional methods of joining different materials together such as soldering, welding, and brazing [Citation132]. The AM approach would optimise the composition gradient of the material in the nuclear plants to ensure that the appropriate microstructure and the right material properties are present for efficient and effective nuclear energy generation. Several government institutions such as the United States Department of Energy Office of Nuclear Energy (US DOE-NE) and independent bodies such as Novatech and BWXT are researching the application of AM in nuclear energy generation [Citation133]. The Nuclear Regulatory Commission [Citation134] invited over 20 companies, standard organisations, and government bodies to deliberate on the application of AM in manufacturing reactor materials and components. Established organisations in the high-value engineering manufacturing space such as Rolls Royce, GE, and Westinghouse are already investigating the possibility of manufacturing next-generation reactors (e.g.. Modular reactors). The International Thermonuclear Experimental Reactor (ITER) for nuclear fusion [Citation133] has focused on using AM process to produce a microreactor. The aim is to reduce the size of the reactor by using the AM process to produce compact parts, saving the space normally required for a nuclear plant. Westinghouse has already installed a thimble plugging device produced via AM in a rector made from 316L steel. Oak Ridge National Laboratory used AM to produce control elements for use in High-Flux Isotope Reactor [Citation135] and Idaho National Laboratory also used AM to produce capsule test samples in an Advanced Test Reactor (Figure 11(b – f)).
For nuclear energy generation, a 3D-printed Fuel component was successfully installed as low-volume, highly critical plant components for current reactor fleets and future advanced reactors (Figure 11(c)). The technological breakthrough promises the possibility of generating safe, clean, and reliable electrical energy for industrial and household consumption. Rosales et al. [Citation15] used AM methods to produce reactor core internal control elements and nuclear fuel. The AM process could be used to manufacture a compact and intricate nuclear fuel and modify the fuel composition by reducing the manufacturing/conversion steps of exotic nuclear materials. Such as the conversion of UF4 to U3Si2 from cradle to nuclear fuel products thereby reducing the amount of material required, steps, and number of equipment required to produce nuclear fuel and also reducing the carbon footprint of the nuclear plant facility [Citation15]. It has already been demonstrated that AM process could be used to reprocess spent nuclear fuel to be reused in nuclear reactors for energy generation. The decomposition of nuclear fuel has been a big challenge in the nuclear industry. The AM process could be used to produce intricate fluid devices within the internal channels of the reactor, which through using centrifugal concentrators can separate actinides from spent nuclear fuel for reuse [Citation14]. The capability of AM to permit recycling and removing actinides from used nuclear fuel would simplify the manufacturing process of nuclear fuels and the generation of nuclear energy for industrial and domestic consumption. This capability of AM to reprocess spent nuclear fuel would halt the debate about considering nuclear energy generation as a green energy source that does not harm the environment (Eco-friendly energy generation source).
It is reported that due to the absence of universal specific codes and standard agreements that are not yet implemented, AM parts that are produced for nuclear plants (Figure 10(b – f)) still remain at the experimental level [Citation133, Citation134]. However, bodies such as the American Society of Mechanical Engineers (ASME), Boiler and Pressure Vessel (BPV) codes for pressure-retaining components, and dedicated units such as the Special Committee on the use of Additive Manufacturing for Pressure Retaining Equipment are formalising the universal agreements that would permit the use of AM parts in nuclear energy generation. It is expected that after the consensus agreements between the various governmental standard boards are met and the respective codes and standards become universal, the AM parts could be used to produce compact microreactors which would permit the production of nuclear energy for various industrial applications. Due to the rapid manufacturing nature of AM, it can be used to produce technology-demonstrator components before full-scale production reducing research and development costs besides other AM benefits as mentioned above.
4. Challenges and future works
One of the main challenges of using AM for manufacturing energy-based devices is the dimensional accuracy of 3D-printed parts. High dimensional accuracy is required for 3D structures to ensure reliability, repeatability, and efficient performance of each device according to the expected standards. Although the various AM process has demonstrated a different degree of maturity it is generally reported that most 3D printed parts deviate from the CAD dimensions [Citation136]. 316L stainless steel bipolar plates with complex structural characteristics termed wine-glass shape were produced by Lin et al. [Citation137] via LPBF. Channels of dimensions below 1.0 mm deviated greatly from the CAD design and demonstrated unacceptable accuracy. Staircase effect [Citation138] begins to occur at an inclined angle lower than 90° and at an inclined angle greater than 90° dross were found on the channel surface which negatively affects the surface quality of the channels. The surface roughness of the channel increases with an increase in the incline angle. There was position variation in the microhardness, molten pool morphology, and microstructure of the wine-glass-shape bipolar plate structure at different inclined angles attesting to the inhomogeneous nature of the LPBF process due to the high energy gradient normally experienced during the building process [Citation139]. The quality of the plates deteriorates with an increase in the inclined angle, increasing scanning speeds, and increases in the width of the structure.
The above-mentioned variation of AM structures from the CAD file is said to be one of the reasons why AM structures are not getting rapid adoption in most energy-based industries as initially anticipated. Apart from not having international consensus regarding standards, AM products are considered less reliable in many high-value engineering industries such as geothermal and nuclear plants [Citation140]. The surface quality of AM samples makes them less agile and acceptable for most engineering applications without post-processing processes – especially for powder-based systems that involve melting of powders to a liquid phase that solidifies to a solid state and goes through thermal cycling layer-by-layer after the solidification process. The manufacturing process induces micro-cracks which are susceptible to defects under severe environmental conditions of energy systems such as nuclear reactors, electrolyses, batteries, fuel cells, and offshore environments. The potential of AM could be industrialised in most energy applications if repeatability of the mechanical properties and surface quality of the intricate 3D structures could be guaranteed. However, due to the touted idea of using AM to produce complex geometries to enhance the efficiency of energy-based devices, bipolar plates such as the wine-glass-shape produced by Lin et al. [Citation137] make it impossible to implement some post-process strategies such as machining, to improve the surface quality. The literature reveals that laser surface modification such as rescanning, and scanning strategies has been demonstrated to improve the surface quality of most AM products to be used in the as-built state [Citation141]. However, the repeatability of the effect of the various scanning strategies on the mechanical properties of the 3D-printed structures could not be guaranteed [Citation142]. For energy applications refractory metals and ceramics are important because materials that can operate at higher temperatures bring higher energy efficiency. However, to date, AM processes such as LPBF, EBM, and DED are not able to produce refractory alloys (Mo, Ta, W, V) without cracking surfaces [Citation143]. The variation in the mechanical properties of AM samples, even within single builds and build-to-build [Citation144], makes it very difficult to standardise the process parameters that can be used to obtain a particular set of mechanical properties for each application. The AM mechanical properties are very dispersed and worsen by the required stress-relieving heat treatment in most cases. Building orientation, scanning strategies, and build chamber parameters among others make the AM samples less reproducible than wrought samples [Citation145]. As a result, adopting the AM manufacturing routes for most energy applications is not favourable. The variation of AM fatigue samples, as a result of surface defects, un-melted powder particles, lack of fusion in the powder, trapped gas, the effect of build-up rate during the build, etc. acting as crack initiation sites have made it worse to adopt the AM process for most energy-based applications despite its promising capabilities to produce complex geometries to enhance the efficiency of renewable energy generation devices. Issues of porosity and residual stress that affect the overall performance of built components, need to be a major research focus to address such limitations. This issue needs to be addressed by mastering the fundamental governing principles of the machine impute parameters, process impute parameters, and powder impute parameters in order to overcome the current limitations [Citation146]. Some mechanical properties of AM printed components are similar or better than the conventionally manufactured counterparts (e.g. Yield strength, ultimate strength), however some critical properties such as e.g. cycle fatigue strength and elongation are significantly below the desired values [Citation147].
Several efforts are ongoing to monitor and control the melting and solidification process by using in-situ monitoring systems such as highspeed cameras, photodiodes, near-infrared thermal complementary metal–oxide semiconductor cameras, pyrometers, etc. [Citation4]. In some instances, multiple monitoring devices are used to generate the necessary computational information to assist in developing process parameters that would ensure repeatability of the mechanical properties and surface quality of AM samples. There is a great need for fundamental research for the AM process to attain the maturity of consistent repeatability of its mechanical properties and surface quality devoid of defects to ensure its application and mass production of energy generation components.
Apart from the in-situ monitoring modelling techniques, numerical modelling methods are also being developed to understand the behaviour of the melting and the solidification process to better determine the optimum process parameters that would yield the ideal results. Finite element modelling, Lattice Boltzmann methods, molecular dynamics method, volume of fluids, and statistical methods are some of the modelling techniques that are used to understand the temperature evolution, residual stress, molten pool dimension, and rapid phase change during the building process [Citation148–150]. What makes it very challenging for the moulding process to correctly predict the ideal process parameters is that during the actual laser melting process, approximately only 30–50% of the laser radiation is absorbed into the powder bed [Citation23, Citation151]. The remaining energy is dissipated through reflection. There is a great variation of the initial molten pool on the base plates due to heat-sink since the base plate is normally at a lower temperature than the laser radiation at the initial stage of the building process. Several strategies have been adopted to ensure the base plate is at the same temperature as the subsequent layers [Citation132]. It is reported that the underlying physics that governs the microstructural evolution and chemical redistribution during the building process is not understood. Further computational, simulation, and modelling of the process are still required to gain an understanding of the governing principles that determine the final 3D-built components.
The challenges AM 3D samples provide are unconventional and require new sets of experiences to address the heterogeneous nature of the mechanical properties and the uneven distribution of defects in as-built components [Citation152]. The variation in the microstructure makes it difficult to predict its behaviours in extreme environments for most energy applications. It is of paramount importance that AM processes are understood and controlled to enable the manufacturing of components with repeatable mechanical properties. There is a need for improved AM models that accurately represent the actual thermal behaviours during the building process to reduce the heavy dependence on experimental optimisation of processing parameters. It is rather unfortunate that most AM mechanical testing methods are conducted in uniaxial testing, not in multiaxial testing detentions. To worsen the situation most of these tests are conducted at or near room temperature [Citation4], whereas for energy applications high-temperature experiment is required. As a result, there is a large gap in comprehending the behaviours of AM samples in harsh electrochemical environmental conditions. Due to the rapid advancement of technology in this era, it is expected that the current energy system environment would increasingly become complex as new technology continues to emerge, and an understanding of AM is equally required to be in tune with the latest developments in the energy industry.
AM has the capacity to innovate the renewable energy sectors in several ways. AM provides value-adding opportunities such as redesigning production tools (e.g. geothermal tools) with internal cooling channels and improving the economic sustainability of energy harvesting machinery. The customised tools could be produced monolithically onsite avoiding the unplanned delays in a supply chain that cause revenue loss that often greatly outweigh the price of individual parts. Although the is a significant amount of energy embodied in the production of powders, especially metal powders and the printing process the direct printing of near-net-shape and the small batch production strategy have reduced material requirements and the chain steps of producing individuals’ parts. In effect, it is reported that the AM process has reduced environmental impacts of supply chains by 25% [Citation153]. The cost of storage and transportation of raw materials, semi-finished products, and finished products are reduced due to the supply chain efficiency of the AM. The design optimisation process reduces the number of components, which reduces the number of external vendors and the bureaucracy of documentation and approval by regulatory authorities throughout the supply chain. The ease of designing and redesigning the prototypes – making the necessary changes and the capability to know the amount of material required and the time for the building process to be completed via the CAD file makes it possible for tracking and planning subsequent jobs with efficiency. Through redesigning and topology optimisation AM has reduced the material used in the final parts of most energy generation machinery by 35–80% [Citation154]. AM has changed the concept of mass production to mass customisation since different designs can be produced on the same machine just by changing the design [Citation155].
Although AM is an intense field of research with new technologies being pioneered constantly, not all AM systems could produce 3D structures to meet the sub-micron resolution features required to meet the specifications of most tools for energy generation. Even AM systems that demonstrate rigorous geometry precision’s print rates are currently slow (<100 mm3/h), with fairly small build chambers [Citation156]. Hybrid manufacturing might help resolve some of the current challenges since the machines can complement each other to achieve the tolerance required. Despite all the current limitations of AM process, its value-added intricate geometry, weight reduction, cooling channel, elimination of assembling process, and less material usage. etc., outweighed all the limitations. Also due to intensive ongoing research, most of these limitations will definitely be overcome. The lack of a validation framework has bred scepticism against the swift adoption of AM-printed parts. It is always a challenge convincing industry practitioners to use AM components since there are no global standards/validation and certification authorities with a consensus voice about the integrity of AM parts to be used in the energy industry. There is also a need to specifically develop high-strength and corrosion-resistant alloys for harsh environments such as deep underground geothermal wells.
Regarding AM solar cells, the manufacturing process needs to be economically competitive with existing manufacturing solar cell technologies to necessitate industrial commercialisation. The current challenges that need to be overcome to make AM economically viable for manufacturing solar cells are: throughput, price, quality, manufacturing speed, small size of AM machine chambers, geometrical precision of manufactured parts, compatibility with existing processes, competitive longevity of service life of AM solar cells, rate of adaptability compared to existing processes, use of sustainable materials for printing, resistance against degeneration, oxidation, and moisture [Citation157]. Although AM might appear to provide a facile route to manufacturing the next-generation solar cells, further research is required to realise the commercialisation of most of the current ongoing development. The challenge of using different AM processes for the deposition of solar cell active materials, conductive and protection layers are still at the research and development stage for most AM technologies. One of the challenges is that some of the materials are very sensitive to oxidation, humidity, or degeneration making most AM systems not technologically ready to be used to produce some components of solar cells. There is a need to develop new materials, and protective atmosphere printing among others [Citation158].
Despite the current maturity level of the AM technology and the success demonstrated, it is not yet a mainstream choice for most energy applications. It is currently mainly used for prototyping and model-making. AM technology remains secondary for most engineering applications, this is because it is replacing tried and tested production methods. AM is a relatively new technology that definitely carries a level of risk that most companies are not comfortable with. A rigorous certification and part qualification process may ease the fears of most companies and a possible rise in the adoption of the technology. The economics of AM favours high complexity – low volume production and just-in-time production. Unfortunately, after the research and development stage, it is the mass production of a particular product that brings economic gains. Economic-of-scale gives the conventional manufacturing process advantage over the AM process in most situations since about 99% of products do not require mass customisation but rather mass production for quick economic gains [Citation159].
As a revolutionary technology, there are several uncertainties such as the health and safety of manufacturing engineers who come into contact with the micron and nano powder particles during the printing process. Issues of intellectual property during co-designing/co-creation process to produce customised parts are still not resolved while using reverse engineering principles to print like-for-like spare parts replacements without permission from the original equipment manufacturer are still on the discussion table.
5. Encouraging results
AM components have already found applications in several energy sectors, such as the nuclear energy sector where AM samples are used to build nuclear core components with significant improvement in material performance and efficiency. Further understanding and control of AM processes could lead to building of advanced nuclear reactors such as small-modular reactors and micro-reactors. The current information reveals that AM samples used in nuclear plants such as steel demonstrated resistance against irradiation-assisted stress corrosion cracking. However, the reasons for the high resistance of AM materials against irradiation-assisted stress corrosion cracking are not yet known [Citation152, Citation160], which requires further investigations.
With the right in-situ monitoring and development process AM materials could be used to print batteries and co-design smart electronic devices (IoT) with embedded sensors. AM has demonstrated its capability to compress the conventional five basic battery layers into three layers. AM could be used to deposit multi-material ink in one pass for batteries demonstrating a good combination of higher power and higher energy. The AM process has been used to produce electrolysers, electrodes, chambers of fuel cells, membranes of fuel cells, and in some instances, AM processes have been used to print a complete fuel cell monolithically eliminating all the assembling and bolting processes. The hydropower plants and geothermal plants have also benefited from AM processes in terms of field manufacturing of components, reduction in inventory due to the onsite manufacturing, rapid prototyping of intricate components, and low turnaround time. The modelling and computation success so far has helped to speed up the initial adoption of AM for some energy applications. Also since AM processes are part of lab automation and digital manufacturing, data collected could be processed by artificial intelligence (AI). The synergy between AI, automated testing, AM process, materials selection, and design would ensure accurate repeatability of experimental processes since humans can be limited in 100% lab automation process. With AI experimental uncertainty would be completely avoided and results from different batches of experiments can be reliable. Nonetheless, the main challenge regarding qualification and global standards needs to be solved. It is anticipated that due to the rapid prototyping nature of AM process, its qualification process would be faster than the conventional manufacturing qualifications and standardisation process. Although AM process could be assumed to gain an industrial level of maturity further research is required for the mainstream application of AM in the energy sector.
Additive manufacturing is one of the pivots of the 4th industrial revolution [Citation161] and has a strong role to play in decarbonising the environment. Apart from all the well-known advantages mentioned above, the main benefit of using AM to produce renewable energy generation devices is to eliminate the reliance on fossil fuels for energy generation. AM is contributing significantly to decarbonising the environment, gearing towards a carbon-free world. The role of AM in energy generation is to optimise the operational efficiency of energy systems, ensuring sustainability and full functionality of energy systems, and constantly improving their technical performance, ensuring management efficiency and financial gains while paying full attention to creating a carbon-free world [Citation162–164].
6. Conclusion
AM has the potential to revolutionise the entire regenerative energy portfolio to satisfy the world's desire of reducing carbon footprint. The customised and miniaturised nature of AM to produce customised energy generating and storage devices such as batteries, FCs, solar cells, turbine blades and downhole tools for the geothermal reservoirs endows them with superior features and performance efficiency. AM is an ideal candidate for producing most renewable energy machinery due to its low-volume production requirements. A large percentage of the global energy generated is consumed by the manufacturing industry and the manufacturing industry accounts for a large percentage of carbon emission. Using AM, which is generally considered a green/clean manufacturing process to produce renewable energy generation devices would have a dual effect in protecting the environment – by the manufacturing process itself and the use of the devices produced. Although AM has demonstrated its unique advantageous capabilities it is not yet the mainstream technology for producing most renewable energy generation devices due to the lack of regulatory framework and the current challenges of inherent variability in the mechanical properties of AM build components leading to non-repeatability and uncertainties in the longevity of AM products.
Acknowledgment
This research was funded by the South African Research Chairs Initiative of the Department of Science and Technology, and the National Research Foundation of South Africa (Grant No. 97994), the Collaborative Program in Additive Manufacturing (Contract No. CSIR-NLC-CPAM-21-MOA-CUT-01), the Manufacturing, Engineering and related Services Sector (merSETA) and Central University of Technology (CUT) MoA: Funding of the Chair in Innovation and Commercialisation of Additive Manufacturing (CICAM), 21 December 2018.
Disclosure statement
No potential conflict of interest was reported by the author(s).
Content Credits : © 2023 The Author(s). Published by Informa UK Limited, trading as Taylor & Francis Group