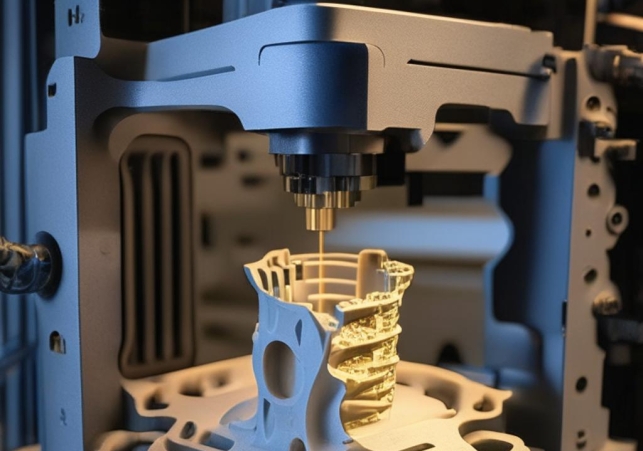
3D Printing for Engineering & Tooling
3D printing has revolutionized the field of engineering and tooling, offering numerous advantages in terms of design flexibility, rapid prototyping, customization, and cost-effectiveness. Here are some key applications of 3D printing in engineering and tooling:
-
Rapid Prototyping: 3D printing enables engineers to quickly produce functional prototypes, allowing for faster design iterations and reducing the time to market for new products. It eliminates the need for expensive and time-consuming traditional prototyping methods, such as CNC machining or injection molding.
-
Customized Tooling: 3D printing allows for the production of customized tooling, such as jigs, fixtures, and molds. These tools can be tailored to specific manufacturing requirements, improving efficiency, reducing assembly errors, and optimizing production processes.
-
Complex Geometries and Lightweight Structures: With 3D printing, engineers can easily create complex and intricate designs that are challenging or impossible to produce using traditional manufacturing methods. This capability is particularly valuable in industries such as aerospace, where lightweight structures and complex geometries are critical for improved performance and fuel efficiency.
-
Functional Prototypes and End-Use Parts: 3D printing has advanced to the point where it can produce functional prototypes and end-use parts with suitable mechanical properties for certain applications. This allows for testing and validation of designs before investing in expensive tooling or full-scale production.
-
Tool and Die Repair: 3D printing can be utilized to repair or replace damaged or obsolete tooling and dies. This can extend the lifespan of tooling, reduce downtime, and eliminate the need for costly replacements.
-
Production of Complex Tooling Inserts: 3D printing enables the production of intricate tooling inserts with conformal cooling channels. These channels help improve the cooling efficiency during the molding or casting process, leading to better part quality and reduced cycle times.
-
Optimization of Part Consolidation: 3D printing facilitates the consolidation of multiple components into a single complex part, reducing assembly requirements and enhancing overall structural integrity. This approach can lead to lighter and more efficient designs, especially in industries such as automotive and aerospace.
-
Prototyping and Testing of Mechanisms: 3D printing enables engineers to create prototypes of mechanical systems, including gears, linkages, and hinges. This allows for testing and refinement of mechanisms before committing to mass production, saving time and costs.
-
Reverse Engineering and Replication: 3D scanning combined with 3D printing enables the replication of existing parts and components. This is particularly useful for industries that require spare parts for legacy equipment or for creating customized components that perfectly fit existing systems.
-
Small Batch Production and On-Demand Manufacturing: 3D printing offers the ability to cost-effectively produce small batches of parts without the need for expensive tooling or minimum order quantities. This flexibility allows for on-demand manufacturing, reducing inventory costs and enabling just-in-time production.
These applications demonstrate how 3D printing has transformed engineering and tooling, providing new possibilities for design, customization, prototyping, and manufacturing. The technology continues to advance, and its integration into various industries is expected to grow in the coming years.